On the south end of Ottawa lies
a demonstration facility that makes ethanol in an unconventional
way. It’s operated by Iogen Corporation, one of the nation’s
biotechnology firms, whose slogan salutes ethanol as the clean-burning
fuel of the future. There are high hopes that the fuel will help
to curb both our gasoline cravings and greenhouse gas emissions
(GHGs).
Iogen’s research manager, Heather Pikor, sits down in the
boardroom to discuss the innovative process and technology, which
was over 20 years in the making. She’s brought in a number
of small jars. The first contains what appears to be chopped up
straw, similar to what you’d find on a barn floor. The contents
of the very last, clear and almost water-like, is ethanol.
" No one else uses enzymes to make ethanol" says Pikor.
"There are no other companies making cellulose ethanol right
now."
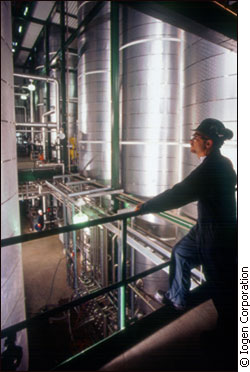 |
A view of cellulose technology at Iogen's
plant in Ottawa |
The privately owned company runs the world’s only demonstration
plant that makes cellulose ethanol, using enzyme technology from
agricultural waste like corn stover, barley, and cereal straws.
Right now, they supply a handful of pumps in Ottawa and can process
up to 20 to 30 tonnes of straw per week. Today, all vehicles can
burn up to 10 per cent of ethanol mixed with unleaded gasoline (E10
blend) without any engine modification.
Pikor says that the problem is fuel production. We have the cars
and infrastructure to use ethanol, but there simply isn’t
enough of it.
Currently, Iogen is working to perfect their process before selling
it worldwide. A move to commercializing its technology could mean
more of this clean-burning fuel.
The unconventional process
Iogen’s novel process begins by adding leftover stover and
straw into a pipe where it's chopped up as if in a blender. It goes
through a high-temperature acidic cook where it’s stewed like
a pot of vegetables. As the fibre becomes soft, all of its sugars
are liberated.
Enzymes, which are non-living proteins, are added to the mix to
help in the chemical reactions. The enzymes occur naturally in a
fungus called Trichoderma reesei, which Iogen grows in
sterile fermenters. After its moves through a natural life cycle
of about one week, it oozes enzymes that are pumped into the pipe.
The enzymes break down the cooked fibre into the familiar liquid
sugar, glucose.
The chemical breakdown takes a few days. Eventually all that’s
left is a mixture of half liquid glucose and another half, a solid-fibre
called lignin. Iogen separates the two and adds
yeast to the liquid sugar, which then ferments into alcohol. The
alcohol is distilled to remove the water, leaving only the purest
form of ethanol. It’s then sold to the pumps and used to make
our engines run while releasing the least amount of GHG emissions.
 |
The large-scale process involves energy heat
integration, water recycling and the use of by-products like
lignin to fuel it. |
The leftover lignin is a crucial by-product of the process. The
fibre is fed into specially made turbines, designed to burn it.
Instead of importing energy to fuel the machines (causing more GHGs),
lignin fires up the process again.
Iogen hopes to boost production by commercializing this enzyme
technology. They have already received worldwide recognition because
they’ve shown in the plant that it works.
Still, Iogen is perfecting the process. Pikor says they hope to
build the first plant by 2007 and each could cost upwards of $400
million. Leading car and oil companies like Volkswagen and Shell
have shown interest, by announcing partnerships to build plants
as far away as Germany.
But Iogen may not be Canada’s only success story. Other
companies are also trying to stir ethanol’s production pot.
By offering a faster process, B.C.’s Syntec Biofuel, shows
that there could be better methods out there.
Syntec has also refined the conventional ethanol-making method
in its five years of research. Lawrence Wong, the principal founder
of the company, says its process is unique and different from Iogen’s.
“Our process is shorter because it has fewer steps. We don’t
have a fermentation stage, which can take days. We make ethanol
thousands of times faster. We can produce it in a matter of seconds,”
he says.
Making ethanol from syngas
Syntec is also not just restricted to making ethanol out of agricultural
waste.
The company can produce ethanol iusing gas from burning landfill,
manure, sewage and wood. For example, Syntec’s process involves
taking sewage and burning it in a chamber to make gas. It’s
then purified through a filter to remove contaminants like carbon
dioxide and nitrogen. The burning produces only five per cent waste.
The ash and char can be used for other things, like agricultural
fertilizer.
Next, the gas is reformed into a mixture of hydrogen and carbon
monoxide called syngas. After it’s compressed, special patented
catalysts are added to turn it into ethanol.
Syntec’s catalysts are multi-metal solids, which are the
driving forces behind the process. The heat released in the method
creates enough thermal energy to start it again like lignin does
in Iogen’s plant.
Wong says Syntec already has two patents on its catalysts. He
predicts that the process will be ready in the next two or three
years.
" Nothing is new about the process except Syntec’s
catalysts. It will be very easy to commercialize because syngas
technology already exists, it’s been used for years and it
works."
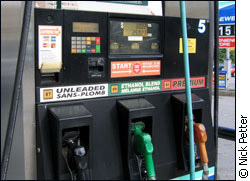 |
MacEwen, Mr. Gas, Sunoco, Suny's, Francis
Fuels and Drummond gas stations all sell ethanol blended fuel. |
Wong is hopeful that Syntec’s technology will change the
ethanol industry because of its low operating costs and quick production
rates. With its innovative technology, production may never be an
issue he says.
Currently, Canada is a net importer of ethanol, says Claude Robert,
a senior economist at the Office of Energy Efficiency at National
Resources Canada.
" We produce about 200 million litres of ethanol a year,
but we import about 125 million litres from the United States,"
he says.
Will new technologies pump ethanol production?
The Canadian government is trying to encourage more production,
Robert explains. Under its $100 million Ethanol Expansion Program
of 2003, it has given financial assistance to build five conventional
plants in Canada.
'Research and development
funding for ethanol technology gets less than biodiesel and
hydrogen.They get only about $750, 000 to $1 million a year
which is low. It’s enough to support about five companies.' |
Robert says the government is also very interested in new technology
like Iogen’s cellulosic process and have discussed with Iogen,
new sites for a commercial plant in places like Saskatchewan. He
cites the government’s interest in new development companies
like Syntec too. It's important in the country’s quest for
more ethanol production and use.
Bill Cruickshank, manager of Biochemical Conversion at Natural
Resources Canada says it takes awhile before new technology is commercialized
to start production.
The funding for Iogen’s research was spread out over a number
of years, and right now government funding isn’t that high,
he says.
"Research and development funding for ethanol technology
gets less than biodiesel and hydrogen," he says. "They
get only about $750, 000 to $1 million a year which is low. It’s
enough to support about five companies."
Wong says Syntec gets about $200,000 a year. Pikor cites Canadian
government support for Iogen’s research over many year including
a $10 million loan to build the demonstration plant. Both companies
also get money from private organizations and venture capitalists.
Syntec’s methods are fast, but Cruickshank says it could
take a long time before companies like it, can start building commercial
plants like Iogen is going to do.
"Iogen’s technology is advanced in terms of maturity
because it started researching years ago," he says. "They
are close to commercialization where other companies like Syntec
may not be at that stage yet. The time and money it takes to reach
that point and build a demonstration plant and test it out, takes
five, 10, 15 and in Iogen’s case, 20 years."
Whether or not these new technologies will really live up to their
production promise isn't known, Cruickshank explains. He says new
technology is always more expensive and so it’s harder for
it to be competitive.
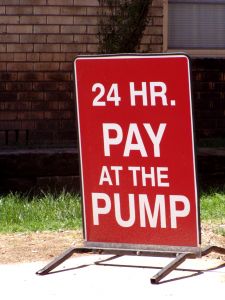 |
Ethanol could become cost-competitive with
government financial assistance and if oil prices remain high. |
"It’s like when new DVD or CD players first came out
it was $1000, now it’s half the price. The price of new technology
eventually always goes down,” he says. "Cellulose ethanol
or Syntec’s technology will be expensive in the beginning
and so will its ethanol because it’s more costly to produce."
Cruickshank explains that we may need some government financial
assistance to build and operate new ethanol plants for it to be
cost-competitive.
"By the time the fifth or sixth plant is built, the price
of the technology and operating it will go down. And if the price
of oil stays high, then ethanol can compete. Companies will start
buying more ethanol to blend and make their fuel."
|