Biodisel: fuel of the future?
By Colleen Kimmett
OTTAWA — The world is realizing
the consequences of fossil-fuel dependance — and
these consequences aren't intangible to the average
citizen anymore.
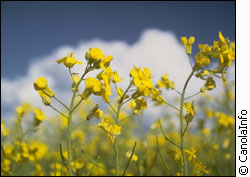 |
Canola plants, above, are just
one possible source of biodiesel. |
When petroleum supplies dwindle, customers pay at the
pump. The country will risk more than it's international
reputation if it doesn't meet Kyoto regulations. Pressure
to comply is also coming from grassroots organizations;
city residents who have more smog warnings each summer
Canada has recently become more interested in biodiesel
fuel, said Dr. Marc Dube, an associate professor of
chemical engineering at the University of Ottawa.
Biodiesel is derived from new or recycled vegetable
oils and animal fats. It burns much cleaner than petroleum,
and is biodegradable. More importantly, said Dube, it
doesn't add to the net amount of carbon dioxide in the
air.
"For example, you've got a field of canola plants
growing, which you turn into oil, which you turn into
biodiesel," explained Dube. "You burn that
in your car and it goes back into the atmosphere as
CO2, which goes back to the canola plants. So it's a
cycle."
Dube and and four other professors at the university,
along with a team of Masters and PhD students, are researching
a new method of producing large amounts of biodiesel.
"When we first started seven years ago, there
was very little interest — at least in Canada.
There was a big industry in Europe, and it's really
established now."
France began producing biodiesel from rapeseed (canola)
oil in the 1990's, using a process called transesterification.
Although any diesel engine can burn pure animal fat
or vegetable oil - like Diesel's crude model at the
world fair - it won't work very well, or for very long.
The glycerol in oil is what causes probems. It is too
viscous, and can clog the parts of a conventional diesel
engine. Transesterification is the chemical process
that cleaves the glycerol from the part of the oil which
is burned.
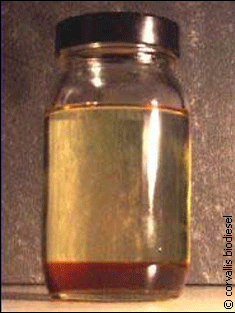 |
The end result: A jar of biodiesel
fuel. |
"The whole goal there is to break the viscosity
down, so it will operate in colder climates, make it
flow better in your engine. Then you don't require any
kind of modification to your diesel engine, you can
just pour this stuff right in there," said Dube.
Traditional separation methods usually leave small
amounts of oil in the biodiesel. The mixture then has
to be diluted with water and "washed." But
Dube said this washing method wastes water and can leave
traces of the catalyst chemicals.
The method that Dube and his team have created eliminates
the washing process. Using what is called a membrane
reactor, the chemical reaction that separates the oil
takes place in a long, heated coil.
The mixture is pumped around the coil and through a
porous membrane. The oil molecules are too large to
pass through, and collect in droplets on the outside
of the membrane.
"They use these membranes for things like desalination,
separating gases," said Dube. "A whole host
of industries have used membranes, but this industry
has not used membranes ever before. This is a patent
we developed."
'We've got it
on a small scale right now. It also works on a medium
scale and it's very easy to bring it to a plant
production scale.' |
Several companies are nowinterested in the model, said
Dube. The simplicity of the reactor design means that
it's relatively easy to adjust. As much as 20 litres
of oil or fat can be processed in about an hour.
Biodiesel fuel is already being used across the country.
Cities like Halifax, Montreal and Brampton all have
public buses that run on biodiesel blend. It's called
B-20; a mix of 20% biodiesel with 80% petroleum fuel.
"That's still a huge, huge cut in emissions,"
said Dube.
Right now in Canada, there are no manufacturers of
biodiesel as most of it comes from the United States.
Dube's research could change that. He says he's not
out to make millions, but wants to sell his technology
to a private company so it can be used to make biodiesel
commercially in Canada.
"I've always been interested in doing research
that's practical, but at the same time, be able to go
to sleep at night and say, well, I'm doing my part,"
said Dube. "It makes me feel good about what I'm
doing.".
|